The modern steel industry is hard to imagine without the ferroalloy field. Since the late 1940s demand for high quality steels and alloys used in aviation and aerospace industry, manufacturing high-tech weaponry, the nuclear industry, power generation and other, began to increase in the world. As the world economy is entering a new level of use of more advanced products with improved quality characteristics, this need increases. And it cannot do without ferroalloys, since the required quality of the valuable types of steel are given exactly by the including to their composition ferroalloys. Each ton of produced metal is added by 10 kilograms of ferroalloys, which significantly improves the structure and properties of steel.
Basic concepts
Ferroalloys are semi-steel products – iron alloys with various elements of Periodic elements system of Mendeleev: manganese, silicon, chromium, tungsten, molybdenum, etc. They are used in steelmaking and other iron-based alloys: for deoxidation (removal from molten metals of dissolved oxygen, which is a harmful impurity which adversely affects the mechanical properties) and alloying (adding impurities to improve the physical and chemical properties) of liquid metal, the neutralization of harmful impurities, for increasing of useful properties of the metal (resistance to stress and wear, etc.), giving it the required structure.
Ferroalloys are divided into basic (largetonnage) and alloying (lowtonnage). The first group includes alloys of silicon (ferrosilicon of all types, crystalline silicon), manganese ferroalloys (high-, medium-and low-carbon ferromanganese, trade and pig silicomanganese, metal silicothermic and electrolytic manganese, nitrated manganese) and chromium ferroalloys (high-, medium-and low-carbon ferrochrome, trade and pig ferrosilicochrome, metallic chromium, nitrated ferrochrome). The second group – ferrovanadium, ferromolybdenum, ferrotungsten, ferrotitanium, ferronickel, ferrokobalt, ferronioby, ferroboron, alloys with rare earth and alkaline earth metals.
The quality of ferroalloys is characterized by: the content and limits of vibration of the leading element in them, concentration of regulated contaminants (carbon, sulfur, phosphorus, nitrogen, etc.), density, surface conditions, melting temperature, oxygen, hydrogen and nonmetallic inclusions. The main indicators of quality are the chemical composition and content in the ferroalloy of main (iron or silicon) and one or more major elements for the purpose of which it is smelted. For example, in low-carbon ferrochrome iron is the main element, chromium is a leading one. Complex ferroalloys contain several leading elements (for example, in ferrosilicochrome this – silicon and chromium).
Methods for producing ferroalloys. A brief description of the process
Currently 4 main ways to get ferroalloys are applied:
1. Electrothermal. Smelting of ferroalloys occurs in arc ore smelting furnaces (continuous processes) or purifying (periodic process) electric furnaces. In ore smelting furnaces ferroalloys are produced by carbon oxide reduction from the ore. All brands of ferrosilicon, carbon ferromanganese and silicomanganese, carbon ferrochromium and silicochromium, etc are produced in them. When refining processes silicon of pig ferroalloys (silicothermic process) or carbon reductant (carbothermic process) are used as a reducing agent. They usually are being done in furnaces of small capacity with the use of pig products and carried out in several stages to ensure the production of alloys of high quality – low carbon ferrochrome, metal manganese, ferrotungsten.
2. Metalthermic. Is based on producing of low-carbon alloys due to the heat of chemical reactions of leading element reduction of the oxides from aluminum concentrates (aluminothermic process), silicon (silikothermic one) or a mixture of aluminum and silicon (alumosilicothermic). It usually takes place in the smelting centers. There is a combined process, when the electric arc heating is used to melt charge stock, and the reduction is carried out by metalthermic scheme. Metalthermic way is used to get ferromolybdenum, ferrotitanium, ferronioby.
3. Electrolytic. Based on the electrolysis of aqueous solutions or molten salts. It is used to obtain high-purity metals, due to the significant expenditure of electricity and the need to use very pure materials.
4. Blast furnace. For the first time it allowed to obtain the necessary ferroalloys of manganese, silicon and chromium. It requires a significant consumption of high-quality coke and received alloys contain a lot of carbon. The disadvantage of this method is impossibility to achieve high temperatures due to the formation of large amounts of gases and losses of heat because of them.
Currently, the most wide spread methods in the world are electrothermic and metalthermic ways. Therefore, ferroalloy production technology is best to be considered in the example of their continuous ore-smelting furnacing in the ore-thermal electric furnace.
The furnace is a cylindrical shaft, where vertically arranged electrodes are based. In general, graphite, carbon and selfsmelting electrodes are used. From above through unloading hopper specially prepared chargе (a set of necessary raw materials) is loaded into the furnace, in such a way that electrodes at all times remain deeply plunged into it. Under the influence of an electric arc under a layer of the charge high-temperature reaction vessel- shaped zone is created, which walls are melted and have a temperature of about 2000 ° C. There are liquid and gaseous reaction reduction products at 2100-2200 ° C inside the vessel. The heat released by radiation in the arcs at the walls of the vessel and due to proceeding of the electric power in terms of the charge from one electron to another. Gradually the charge goes down to the zone of direct reduction. Due to heat exchange with gas the charge is well heated. For a uniform penetration the charge of furnace can be equipped with a mechanism of the tub rotation. Produced metal and slag are tapped from the furnace periodically, as they are accumulated, through the discharge chute.
Ferroalloy furnaces can be the following types: by purpose – reduction and purifying, by construction – open, half-closed and sealed, by type of bath – with stationary and rotating baths, by the form of furnace bath – round, rectangular, triangular and oval, by the method of discharge of alloy and slag from the furnace – motionless, leaning (to produce an alloy quickly and easily) and oven with roll-out bathtubs, by type of supply line – single phase (are of limited use) and three-phase, by the number of electrodes – 1, 3 and 6 (large capacity ovens); by location of electrodes (for three-phase furnaces) – into a single line (rectangular) or the position of the electrodes at the tops of the triangle (round or triangular).
Furnaces for purifying processes are close to the electric-arc furnaces in their construction.
The history of ferroalloys production
According to scientists, the process of removing contaminants from metals and alloys, and alloying them, started in the Bronze Age. That times it was done empirically, basing on observations. It was noticed, that the addition of certain substances in the melting process makes the final product of better quality.
By the beginning of the XIX century ferroalloys from ore was smelted in small quantities and only in blast furnaces. The development of electric smelting was initiated by a Russian scientist Vladimir Petrov, who in 1802 discovered the phenomenon of an electric arc. He was the first to have shown the possibility of using electricity for production processes, as well as carried out heating and melting of various metals by means of an electric arc, and reduction of metals from oxides. In 1856, English metallurgist Robert Myushet acquired a patent with recommendation to add a portion of a mirror iron containing 15-20% manganese into the liquid metal to improve the quality of the cast steel. This is how the operation of deoxidation appeared. The following year, basing on this technology the first batch of long steel rails was made and put on the central railway station of the city of Derby, in the most intensive part of the route. During the 16 years of service more than 1.2 million steam engines and 2.5 million cars have driven on that area. Although, according to the practice of that period, the rails were to be renewed every 3-6 months.
In 1868 Myushet for the first time included tungsten (5.44%) as an alloying element in steel. And from that time steel became able to withstand a red heat, not only maintaining but also increasing its hardness, that is, obtained the property of selfhardening. After 3 years commercial production of this steel for the manufacture of cutting tools for metaltool machine began at the Osbern factory in Sheffield. It was a real breakthrough in the industry and came to be known as “Myushet’s selfhardening steel “. Respectively, ferroalloys for it were required to be produced on an industrial scale. By that time due to the energy development, their reduction smelting in coreless induction furnaces had been mastering and widely using.
In 1882, English metallurgist Robert Gadfild discovered manganese steel. It contained 12-14% manganese, had good castability, wear quality, high resistance to impact and abrasion. “Gadfild’s Steel ” was the first steel alloy of mass production, which came in our time without major changes in its chemical composition.
As for the melting furnaces (including those for ferroalloys production ), at the turn of XIX-XX centuries, their projects have been continuously improved, energy of electric current has been used more widely. The prototype of the modern electric melting furnaces was invented in 1899 by French engineer Paul Arou an arc furnace direct action with two vertical electrodes, supplied to the metal bath. In 1900 in the factory at the Savoy it gave its first products, and for a few next years supplanted the other furnaces, which were less successful in structural terms (with hearth electrodes, graphite crucible, indirect heating furnaces, etc.).
The development of the ferroalloy industry in USSR
Tsarist Russia almost did not make ferroalloys. Low-persentage (as alloying metal) ferro-silicon and ferromanganese were produced at several blast furnaces of metallurgical enterprises of the south of the country. In August 12, 1910 near Satk town (176 km from Chelyabinsk) the first and only one in pre-Revolutionary Russia electricferroalloy plant “Thresholds” started. In its furnaces about 500 tons of ferrosilicon, high-carbon ferromanganese and ferrochrome were smelted annually. It could not ensure the needs of the country’s industry in ferroalloys, so the main part of them was to be imported from abroad.
The same situation existed in the first years of Soviet power. In April 1929 a decision on the first ferroalloy plant in the Soviet Union construction in Chelyabinsk was made. On November 7th of that year the foundation of its shop №1 begun, the next year the first furnace produced the first tons of ferrochromium, and on July 25th, 1931 State Commission took shop in operation.
History of the ferroalloy industry of the USSR dates back to Zaporizhye Ferroalloy Works (ZFW). In 1931, on the Dnipro Hydroelectric power plant which was erecting that time, construction of a large industrial combine of ferrous and nonferrous metallurgy began. The main building was the Dnieper industrial combine, which includes ferroalloy plant. In addition to smelting manganese ferroalloys (given the huge reserves in the region of manganese ore in Nikopol deposits), also production of silicon and chromium products was foreseen. On October 10, 1933, in a year after starting DniproHEPP, two furnaces gave first ferrochrome. Construction of the ferrochrome shop with 5 furnaces was completed in August 1934. Construction of the ferrosilicon shop was going in parallel, the first furnace of which was put into operation in February 1934. Since 1939, ferroalloy production was allocated to a separate plant. By the beginning of the World War II in its 2-smelting shops 11 furnaces were working in which more than 50% ferrosilicon and about 45% of purified ferrochromium of their total production in the USSR smelted.
After the war, ZFW was fully restored by 1951, and in the same year the production of ferroalloys in the company exceeded the prewar level. In 1955-1956 shops № 3 and № 4 were commissioned.
To meet the growing needs of the USSR metallurgy in ferrosilicon, in 1952, it was decided to build a new ferroalloy plant. Work began in 1959, in Kadievka city of Voroshilovgrad region (today – Stakhanov city of Luhansk region). The construction of the plant in this place was due to close metallurgical manufacturers and developed transport communication. On April 10, 1962 furnace № 1 gave the first production, and in November last two furnaces (№7 and №8) of the enterprise was put into work.
In December 1961, the USSR Council of Ministers adopted a special resolution in the construction of plant for the production of manganese ferroalloys in 3 km north-west direction from Nikopol city (Dnipropetrovsk region). The Date of birth of the plant is considered to be March 6, 1966 – the day of starting the furnace № 1 of fluxmetalsmelting shop, completed by the end of June 1967. Commissioning of planned facilities solved the problem of providing engineering and pipe factories of Ukrainian SSR and the USSR welding fluxes of electroslag remelt process. On August 27, 1968 shop for the production of manganese alloys entered into service.
Pobuzhsky Ferronickel Plant became the first and only company in the former USSR, which produced ferronickel on an industrial scale from poor oxidized ore coming into the recycling without enrichment and ball milling (line processing). Along with the untreated ore, processing of finely devided metal-containing wastes (dust, sludge, iron shavings, spent catalysts, etc.) was provided, followed by extraction of nickel, cobalt, chromium, manganese, vanadium and molybdenum in the complex alloys based on iron, used in the future for smelting high-resistance iron, alloy and steel. This technology is characterized by simplicity, multifunctioning, no wastes, environmental cleanliness. The plant was built in the village Pobugskoe of Golovanevsk district of Kirovograd region. The first part of the plant was commissioned in December 1972, the second one – in November 1973.
At the end of 1991 Ukrainian ferroalloy industry had more than a dozen companies actually or potentially producing ferroalloys. In addition to the above mentioned, they were, in particular, Ilyich chemical-metallurgical factory of Mariupol, Steel Plant (its products – ferrovanadium, ferromolybdenum and ferrotungsten), Zaporozhye Titanium and Manganese Plant (manufactured, among other things, ferrotitanium), Constantine and Kramatorsk metallurgical plants (manganese ferroalloys produced in blast-furnace way), etc. The presence of developed ferroalloy industry in conjunction with a strong resource base (over 30% of world deposits of manganese ore and the world’s largest Nikopol manganese basin) allowed to be optimistic about the future.
Production of ferroalloys in Ukraine (post-soviet period)
The Soviet Union occupied the first place in the world in the production of basic ferroalloys. Its ferroalloy industry was focused on the providing of national economy by ferrosilicon, ferromanganese and silicomanganese. In the first years after the collapse of the Soviet Union ferroalloy industry of independent Ukraine (as well as the entire mining and metallurgical complex) was subjected to two trends: first, there was collapse of management and economic relations of the Soviet type, and, secondly, there was a chaotic search for forms of economic activity, which would be adequate to new conditions. Despite the continuous supply of a significant part of its products to domestic and Russian metallurgical enterprises, Ukrainian ferroalloy industry had to find alternative export markets. All the more so in the circumstances of chronic non-payment and netting for ferroalloy plants export remained the only source of “real” money.
Gradually, the share of exports has become a rather weighty, which determined the complete dependence on conditions in foreign markets and the world’s major competitors. For example, until recently ferrosilicomanganese production prevailed in Ukraine. The reason was the rise in prices for that ferroalloy in the world, which reached by the year 2008 the level of $ 2,500 / t. Then the market was overloaded and declining of demand began, causing prices fall. And now ferroalloy workers tend to move from ferrosilicomanganese production to ferromanganese and ferrosilicon ones.
It should be noted that a trend towards a decrease in production of manganese raw materials for ferroalloy production appeared in Ukraine, with a simultaneous increase of its imports. The reason is non-optimal technology quality of concentrates from Ukrainian ore (low manganese and high phosphorus concentration). In particular, against the background of increasing production of manganese resources in the world in 2002-2005 to 2 million tons (25.6%), its production in Ukraine in this period decreased on 120 thousand tons (14.3%).
There also were problems at ferroalloy plants. Thus, in June 1996 because of variety of reasons Pobuzhsky Ferronickel plant completely stopped. Only in March 2001, after a 5-year break, it was restarted. Then the plant experienced a local man-made disaster, the two bankruptcy proceedings. From September 2003 till March 2004 due to high electricity prices the Stakhanov Ferroalloy Plant didn’t produced ferrosilicon. Constantine and Kramatorsk metallurgical plants completely ceased production of manganese ferroalloys using blast furnace method.
And yet, despite the problems and difficulties, Ukraine has taken a leading position in the global market of ferroalloys. The basis of the ferroalloy industry of the country is the so-called “big three”:
* Nikopol Ferroalloy Plant – the most powerful enterprise in production of manganese ferroalloys in Ukraine and one of the largest in the world (over 11% of world production of ferroalloys), the main product is a ferro-and silicomanganese;
* Zaporozhye Ferroalloy Works – one of Europe’s largest producers of ferroalloys (its share in world production amounts to 5.7%), the monopolist in the CIS in ferrosilicon production, and the only Ukrainian producer of intermediate carbon ferromanganese and 90 -percentage metallic manganese;
* Stakhanov Ferroalloy Plant – specializes in the production of siliceous alloys and is the largest Ukrainian producer of ferrosilicon.
In 1997, these companies with Ordzhonikidze mining and processing combine (MPC), Marganetsk MPC and Kharkov Scientific-Research and Design Institute “Giprostal”, created the Ukrainian association of ferroalloys producers (UkrAFP). Its main objectives are to prevent antidumping processes for the supply of Ukrainian ferroalloys in the countries of the world, representation and protection of the founders in the governmental and international organizations, coordination of manufacturers of ferroalloys in the foreign market, etc.
Crisis and post-crisis period.
The economic crisis that broke out in Ukraine in 2008 significantly affected the ferroalloy industry. As a result, in 2009 production in the ferroalloy industry decreased by 27.5%, capacity utilization fell below 50% and selling prices for finished products was reduced by one third. Especially difficult situation was in the segment of ferromanganese, which gave up in comparison with other alloys both in economy of production, and in versatility of use – here the volumes of production made just 35.8% from 2008 index. Ukrainian metallurgical enterprises warehouses accumulated monthly and more ferroalloys stock, in addition, about 1.5 million tons of steel was accumulated in the ports of Ukraine, which was first necessary to sell, only to resume the production of steel and, therefore, of ferroalloys. The situation in the world markets was not much better.
With the improvement of world metal markets conjuncture the industry became gradually recovering from the experienced shock. By the end of 2010, Nikopol Ferroalloy Plant has increased the load on its capacity to 90%, at the Zaporozhye ferroalloys plant output of production increased by 33.5% in comparison with 2009.
Balance of ferroalloy market in Ukraine, thousands. tones:
2008 | 2009 | 2010 г. | |
Production | 1410 | 1022 | 1423 |
Export | 993 | 698 | 1001 |
Import | 106 | 128 | 75 |
But in 2011, a new serious problem appeared – the dominance of foreign importers in the Ukrainian market of ferroalloys, when 3 years ago they occupied only about 5% of the market. Now, for the first 8 months of 2011, compared to the same period in 2010, imports of ferroalloys increased for 2.2 times – up to 157.2 thousand tons. In terms of money -it’s 377 million dollars. If in the past year the interest of imports (in value) did not reach 25% of the domestic market of ferroalloys, the current one exceeded 50%.
These changes had an immediate impact on the Ukrainian ferroalloy enterprises, which in January-August 2011, compared to the same period of the last year, have reduced production by 13.7% – up to 832.3 thousand tons. In particular, the production of silicomanganese decreased by 7.3%, of ferromanganese – by 32.4%, a 45-percent ferrosilicon – by 17%, metal manganese – by 9.5%. In this case, Nikopol Ferroalloy Plant has reduced production by 12.1% – up to 546 thousand tons, Zaporozhye Ferroalloy Works – by 29.5%, to 139 thousand tons.
Specialists of “Derzhzovnishinform” center believe that by the end of this year, the decline in ferroalloy production in the Ukrainian ferroalloy plants will exceed the last year index by 10-12% and reach 1.3 million tons.
Production of ferroalloys in Ukraine (2009-2011)
In 2010, ferroalloy plants in Ukraine increased production of ferroalloys by 38.1% compared with 2009 – up to 1.432 million tons. However, for 8 months of 2011 compared to the same period in 2010 in Ukraine production of ferroalloys decreased by 13.7% to 832.3 thousand tons.
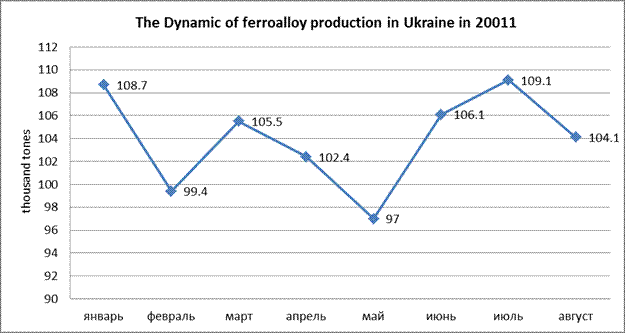
In terms of major products the situation is as follows:
– production of silico-manganese decreased by 7.3% to 583.6 thousand tons,
– production of ferromanganese fell by 32.4% to 132.6 thousand tons,
– production of ferrosilicon (in terms of 45-persantage one) fell by 17%, to 107.5 thousand tons,
– production of manganese metal dropped by 9.5% to 8.6 tonnes.
For 8 months of this year Zaporozhye Ferroalloy Plant has reduced production by 29.5% to 139 thousand tons.
For 8 months of this year Nikopol Ferroalloy Plant has reduced production by 12.1% to 546 thousand tons.
For 8 months of this year Stakhanov Ferroalloy Plant increased its production by 0.5% to 147.3 thousand tons.
Imports of ferroalloys in Ukraine
Until 2009, imports of ferroalloy production in Ukraine was small, its share in total consumption of iron and steel enterprises did not exceed 10%. However, for the period from the third quarter of 2008 to third quarter of 2009, imports of ferroalloys increased by 219%. It is noteworthy that this occurred against a reducing the consumption of ferroalloy production by metallurgical enterprises of Ukraine by 59%.
And in 2011 there was another round of increase in imports of ferroalloys in Ukraine. Thus, in the first half of 2011 imports of ferroalloys in Ukraine increased over the same period of 2010 by 2.1 times, amounting to 110 thousand tons. Cumulative value of imports reached $ 265 million. Monthly, Ukraine is imported more than 25 thousand tons of ferroalloys. If last year the share of imports amounted to 24.75%, in the first half of 2011 the volume of imported goods in physical terms was 51.38% of the domestic market. We see all the signs of expansion importers. This is a dangerous trend for the domestic ferroalloy industry.
According to experts, the continuation of ferroalloys imports growth in Ukraine could have extremely negative consequences. So, Ivan Dzvinka, analyst Eavex Capital, said: “The fact that the supply of imported products undermine the position of domestic producers of ferroalloy production – is obvious. Naturally this is very bad because it leads to monopolization of the market by the importer. We know where it may lead from importers of petroleum products. Having fixated in the Ukrainian market, the importers of petroleum products began to dictate their own terms and monopoly inflate prices. It is known that domestic producers can always be agreed with, but with importers – no. Therefore, it is desirable for the government to create favorable conditions for domestic ferroalloy enterprises. “
However, at present, ferroalloys imports in Ukraine is carried out very intensively. This is discordant with the statements and declared intentions of the government. So, September 12, 2011 Cabinet approved the “State program of development of domestic production,” which declared the purpose of supporting the export and import substitution. According to First Deputy Prime Minister and Minister of Economic Development and Trade of Ukraine A. Klyuev, the implementation of the first phase of the program will help, by 2015, to achieve a positive balance of trade in goods and services at the level of 1.5-2 billion.
But in reality, in key industries today wу see displacement of domestic producers from the Ukrainian market. The result of these ill-considered action – the decline in output by Ukrainian enterprises, reducing their contributions to the budgets of various levels, forced layoffs, growth of import dependence to critical levels, increased demand for foreign currency to import the acquired goods, to some extent fueled by the devaluation expectations.
A striking example of lack of support of domestic producers is the situation in the production of ferroalloys. Control over the Ukrainian market of ferroalloys production is gradually transferred to the companies from Macedonia, France, South Africa, India, South Korea and other countries. Ukrainian metallurgical enterprises have an increased demand for foreign currency for imports of ferroalloys.
There is no economic ground for a major increase in imports of ferroalloy production – Ukrainian producers are able to offer domestic metallurgical plants all the needed line of ferroalloy production, which meets the quality and price parameters of steel mills.
According to analysts, the current situation does not meet the state’s interests. Thus, the head of corporate ratings of rating agency “Credit Rating” Alex Chernorotov believes that “the increase in imports causes an increase in dependence of metallurgical enterprises of Ukraine (as the main consumers of ferroalloys) from prices set by importers as well as the appearance of additional currency risks. In addition, due to rising energy prices, respectively, the competitiveness of Ukrainian products decreases. As a consequence a reduction in the volume of exports from Ukraine and the partial loss of markets happen. All of the abovementioned factors withoutdoubts negatively affect the trade balance of the country and as a result, the stability of the national currency. “
Ferroalloys – is not stock commodity, price environment in this market is largely determined by fundamental factors of supply and demand, not by speculative and psychological factors. This is – a more predictable market. That is why the state should not contribute to the destabilization of this market.
It would be logical if the government will hold a special investigation on imports of ferroalloys, according to the results is useful to implement the regime of ferroalloys import quotas in Ukraine.
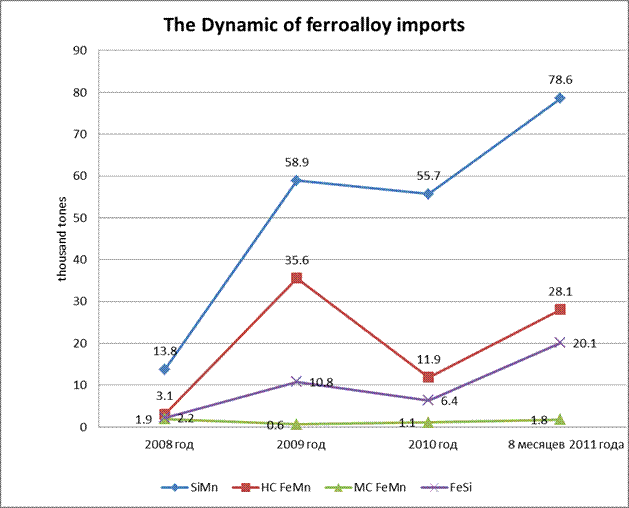
The reasons for reducing the share of domestic ferroalloy in the domestic market of Ukraine
One of the reasons for the decline of domestic ferroalloy production volumes is not impeding its imports. Besides, uncontrolled growth in imports and a decrease in production volumes of Ukrainian ferroalloy plants are mutually supportive in nature, creating a negative synergistic effect.
In its turn, the decline in the production of ferroalloys in Ukrainian enterprises has forced nature. It is due to ruinous as a whole for the ferroalloy industry policy in electricity tariffs creation, but also because of ill-considered claims in matters of environmental compliance.
At the time, when ferroalloy plants in other countries are stable, domestic producers of ferroalloys have to stand because of high energy costs and monopolistic pricing in the electricity market. This view is shared by economic experts. For example, Arthur Ogadzhanyan, partner at Deloitte & Touche, said – “Because of the high electricity prices, Ukrainian ferroalloy enterprises have to reduce production volumes, reduce revenues to the state and local budgets, reduce production, demand for foreign currency increases. Of course, this is not normal. State support for energy-intensive industries should be in particular, as well as providing support to domestic producers as a whole. “
In Ukraine, there is no direct contracts between producers and consumers of electricity (which contradicts with the ‘Third EU energy project “under which the buyer must be provided with free choice of electricity suppliers). All electricity is sold on the wholesale market, where its price is averaged, with a focus on the highest of the proposed prices.
Consumers of electricity, depending on the volume of electricity consumption are divided into two classes. The division into classes of consumers is regulated by the NERC Decree № 493 of June 30, 2005. The first class – are industrial enterprises with an average monthly consumption of at least 150 million kWh. The second class – are the people and businesses with an average monthly consumption of less than 150 million kWh. For them, the cost of electricity is more expensive by 30-35%.
If a large enterprise is transferred to the second class of consumers of electricity, it loses a significant degree of competitiveness (because of increased production costs). This can be illustrated by the Zaporozhye Ferroalloy Plant (ZFP). Problems have arisen in ZFP in early 2011. Causes of problems – translation into the second class of consumers of electricity and refuse of “Zaporozhoblenergo” to extend the company the right to lease the lowering substation the “F-2” (due to lease of the substation till the end of 2010 the plant received a significant portion of electricity according the first class), which is located in the territory of the plant.
Since the beginning of this year NERC, displaying a formal approach to the issue, transferred ZFP to the second class of electric power consumption. It explained its decision that the power company is lower than those needed for the first-class 150 million kWh per month (in 2010 the average monthly consumption of ZFP fell to 136 million kWh, although in December amounted to 148 million kWh, which is only 1.3% less than the norm for the first class of consumers). Reducing of energy consumption by the factory has been caused by objective reasons – from mid-June to late August 2010 the company operated at 28% capacity because of unfavorable market conditions in the markets of metal products. Since the beginning of 2011 ZFP has paid for electricity about $ 0.12 per 1 kWh, while customers of the first class – $ 0.07.
Due to the fact that the cost of electricity in the production costs of ZFP reaches 54%, profitability of production was reduced to a minimum. Therefore, the company had to stop production capacity. Transfer of the factory to the second-class power consumption is unjustified from an economic point of view, Alexander Hudyma, a member of the Verkhovna Rada Committee on Energy, Nuclear Policy and Nuclear Safety, said – “Zaporozhye Ferroalloy Plant pays hundreds of millions of hryvnia for electricity. Logic dictates that it should be transferred to consumers of the first class. Without this plant, the entire steel industry of our country can stop. But, surprisingly, strange and inadequate action are takenby the NERC. It is obvious that someone close to the current government just wants to bankrupt the ZFP, and then lay his hands on it.
After the cost of electricity for the ZFP has grown by 25%, the monthly expenses of the enterprise on its purchase increased by 20 mln. In particular this is connected with the fact that the ZFP specializes in the production of ferrosilicon – ferrosilicon production is one of the most energy-and material-intensive within basic ferroalloys. Thus, consumption of electricity to produce 1 ton of alloy FS65 is 7100-7500 kWh, for FS75 – more than 9,500 kWh, and for manganese alloys – from 3000 to 5000 kWh.
As of October 2011 from the 31 ferroalloy furnaces of ZFP 15 furnaces were shut down. As a result, for the first 8 months of 2011, compared to the same period of the last year, the output of the company decreased by 29.5%.
Analysts of the stock market say that actions of regulatory authorities are not adequate from an economic point of view. So, Maxim Shein, chief investment strategist at IC “BCS”, says – “It seems that the Ukrainian state purposefully destroys his ferroalloy industry in favor of the industries of other countries. Confirmation of this is a refusal to grant Zaporizhia Ferroalloy Plant the status of consumer of electricity of the first class. Of course, this is no good. Due to the forced reduction of output in ferroalloy plants in Ukraine revenues to the state and local budgets are reduced, revenues from taxes on personal income falling, the load on the employment fund increases. Such a policy is highly undesirable. Such problems may lead to budget deficits. “
It should be noted that because of the questionable in terms of economic logic increase of the price of electricity for one of the largest producers of ferroalloys was not only a drop in production of the product and increase its imports to Ukraine, to the extent that threatens the future of domestic ferroalloy plants. The decision to transfer ZFP to the second class of power consumption caused damage to the electricity industry.
According to specialists ZFP, the NERC suggested that due to the transfer of ZZF to second-class power consumption, the company will pay for it extra 184 mln hryvnia for the year. In fact, due to the forced reduction of consumption of electricity, the payments are not increased and, conversely, decreased by 52 million hryvnia per month – when in December 2010, ZFP worked for 70% of the project capacity, now because of the unnecessarily high cost of electricity, the plant operates at 40% of capacity. Accordingly, power consumption has fallen sharply. If the trend of 8 months of 2011 continues, the by the end of the year ZFP will buy electricity for 625 mln. hrn. less, than it could if it got to the first class.
Regulator actions are criticized by the leaders of investment companies. So, Vladimir Sirenko, CEO of IC “Prospect Investments,” said – “From my point of view, the state now operates in the interest of power engineers, rather than producers of ferroalloys. But in the end it turns out that it is killing both of them, because “Zaporozheoblenergo” has not received increased sales due to the fact that Zaporizhia Ferroalloys paid at the rate of second-class power consumption. Maybe the power represented by NERC just playing up to businessmen close to it, destroying the business owners of ZFP. Then a pro-government oligarchs will buy the plant at a low price and for him the price of electricity will be decreased very quickly. That is, perhaps, this scenario is the redistribution of property. “
At the current level of tariffs Ukrainian enterprises are unable to price competition with foreign producers on foreign markets. As a comparative basis we present the following data: ZFP now pays $ 0.12 per 1 kWh. At the same time, the company BHPB Meyerton (South Africa) – 0.058 dollars per 1 kWh, the company Eramet Marietta (USA) – 0.0424 USD per 1 kWh, the company Ferroatlantica (Spain) – 0.0631 USD per 1 kW Ah, the company Sabayek (Saudi Arabia) – 0.032 dollars per 1 kWh.
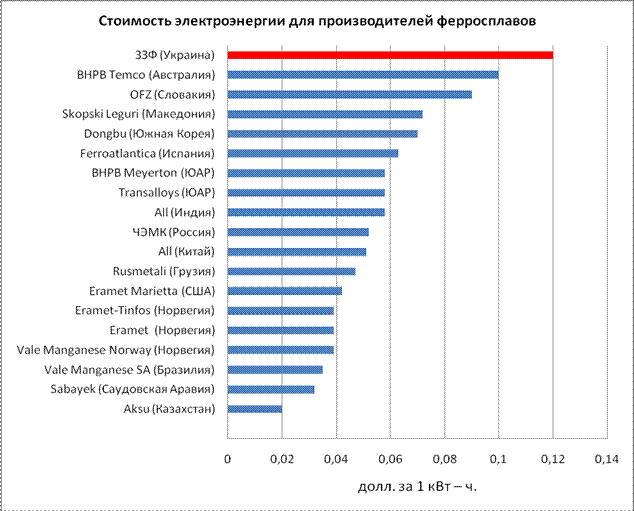
It should be noted that government support of energy-intensive industries has been used successfully in civilized countries. We are talking about support to key enterprises for the state economy, special tariffs for electricity for which stimulates economic growth.
Thus, the average price of 1 kWh of electricity for industrial consumers in China is 0.059 USD in Japan – 0.056 USD in the U.S. – 0.054 USD, in Russia – 0,035 USD , in Kazakhstan – 0.03 USD. In Ukraine industrial enterprises operating in the second class of power consumption, pay for 1 kWh $ 0.12. In such conditions, Ukrainian ferroalloy plants can not compete with foreign companies – both in domestic and foreign markets.
Functioning system of Ukrainian electricity market
In addition to formal, irrational approach to tariff setting, there are the problems in strategic plan of cross- price subsidization and monopoly pricing power in the Ukrainian market.
Tariffs
Electricity tariffs are approved by the National Energy Regulatory Commission (NERC). They are calculated by a specific method approved by this body. The amount paid by the consumer, is the cost of electricity, the cost of its delivery and the transfer (this includes also expense item for the maintenance of networks in the desirable state). Every company which has a license to supply electricity and electric networks exploitation, calculates its own extra charges, but they are approved by NERC.
The current model of the electricity market
The electricity market of Ukraine was established on the basis of the Agreement between the members of the Wholesale Electricity Market of Ukraine, which was signed in November 1996. Problems that hinder the effective functioning of the wholesale electricity market are linked with one another, often share common causes, which affect not only the functioning of wholesale electricity market, but are problems of macro-economic level – in particular, shortcomings in the system of public funding of preferential consumption of electricity, non-optimal tax policy on the electricity industry, an attempt to solve the problems of industry and agriculture, as well as social problems at the expense of electric power.
Wholesale Electricity Market (WEM) is designed to function as a pool with a mandatory schedule of load on the next day, in which on the basis of the application highest price establishes a maximum price of the system. It does not stimulate the formation of an optimal price.
In Ukraine, there are seven main generating companies – one hydroelectric, one nuclear and five thermal generation companies, and it is the latter shall establish the maximum price. It is clear that the cost of thermal generation in a number of reasons is the highest, that in the existing system of organizations WEM properly affects the final prices for consumers. Due to high cost of electricity generated at thermal power plants, the negative economic effects are felt by metallurgic industry enterprises (including and ferroalloy plants).
Electricity market reforming
Market of bilateral contracts for electricity supply, namely, it the current WEM was planned to be upgraded into it (talked about that it would have done in 2008, but in reality progress in this direction is not up to the present), compared with a pool, has clear benefits. It allows participants to set the volume and price together with the reduction of risks. The market of bilateral contracts for electricity is more transparent, ensuring consumer confidence in the fair prices. It is able to reverse the conditions for the manipulation of electricity prices, complicating the possibility of individual producers to set a profitable for them only price for all the market.
Bilateral contracts market also offers significant advantages in cases where there is a problem of administrative interference in the markets of electricity (which is observed in Ukraine). In turn, the central market, such as pool, contributes to such actions.
Decentralized market reduces the possibility of taking advantage of each player of the electricity market at the expense of consumers. Increased transparency in the operation of the electricity market due to the transition to the market model of bilateral contracts will significantly increase the investment attractiveness of Ukrainian electric power.
This view supports Maxim Shein, chief investment strategist at IC “BCS”, who said: “Ukraine has to change organization of the electricity market. Atransition to a market of direct contracts and accession to the European Energy Community are needed. This will attract new investors from EU countries. “
Bilateral contracts market in comparison with the pool, in the form of WEM working today, has the following advantages:
– It allows participants to set the volumes and prices with a reduction in their operational risks;
– It is more transparent, providing confidence in the fair price results.
A full-scale competitive wholesale electricity market, which is based on bilateral agreements, covering a number of markets with different time intervals, as follows:
– The market of long-term contracts, where buyers and sellers of electricity enter into contracts for the supply of electric energy in the future. As a rule, they can be concluded for a week, month or year;
– The market “for the previous day” on which buyers and sellers enter into contracts for the supply of electricity for the next day at certain periods of time, or at all times with a focus on cost price of electricity for the previous day;
– The balancing market. It is used for supply balance and demand for electricity (balancing system) in real time throughout the day.
An additional point which should act to increase the efficiency of electricity distribution companies will be that due to the reform of the WEM, a competitive electric power supply by third parties will be allowed.
With a view to reform WEM to transition to a model of direct contracts between generating companies and consumers and creating balancing market the following should be done:
– Relative to sale of electricity under direct contracts it is desirable to conclude such agreements with companies that have large amounts of scheduled electricity consumption in the zones of a day (including – ferroalloy plants);
– Legislative formalization of permits for any generating company, which power is not involved in the balance of energy system in Ukraine, to sell surplus electricity for export under direct contracts.
In the direction of improving the efficiency of the pricing system for electricity is expedient to implement the following activities:
– The transition from expendable method of forming the electricity tariff on a methodology that will encourage energy companies to increase production of electricity and reduce its cost;
– The electricity tariff should take into account the costs that power generating companies implement into long-term exercise programs.
In addition, from the perspective of Ukraine’s economy needs it is necessary to provide special tariff for industrial consumers of electricity, paying special attention to those enterprises that consume large amounts of electricity by technological necessity. Special tariff is to be extended to companies that have the following distinctive features: high power consumption because of production technology, limited by strong market conditions the profitability of production. These include producers of ferroalloys.
This view is shared by stock market professionals. In particular, Vladimir Ovcharenko, IC KINTO analyst, says – “From the standpoint of the competitiveness Ukrainian ferroalloy plants need a reduced tariff. If only because the world ferroalloy enterprises enjoy preferential tariff and if we want to be competitive, we must also introduce a similar rate. The state should seek to protect its own producers, as it is done all over the world. Otherwise, it is hard to understand – why we need state if it fails to protect its own economic interests.”
Given the high share of energy costs in the cost of production of ferroalloys, special rate is appropriate to be set at a level that would have been lower than for companies that buy electricity at a first class consumption. In civilized countries special rates for the ferroalloy industry are used.
Reduced electricity rates for ferroalloy industry enterprises will lead to an increase in electricity consumption, hence, the amount of payments for electricity will increase. This will benefit the state, as in the capital of Ukrainian power generating companies, a substantial part belongs to the state.
The problems with environmental requirements
Ferroalloy enterprises in Ukraine are made unnecessarily great environmental demands that dissonant with the state attitude to enterprises. At the same time, feasibility, simplicity and concreteness of environmental legislation is essential for the successful operation of an industrial enterprise in solving environmental problems and tasks to minimize the negative impact on the environment. At the present time is not properly to say that the Ukrainian legislation meets these requirements for a number of the following reasons.
According to the type of environmental impact ferroalloy producers, as well as any industrial enterprise of the metallurgical complex of Ukraine, mainly influence upon the air, water objects, the formation and deployment of industrial waste.
The biggest problem of ferroalloy enterprises in Ukraine in the sphere of environment is the air pollution by industrial emissions, consisting of manganese dust and gases (carbon monoxide, nitrogen oxides, sulfur dioxide). On the second place by importance is the problem of waste in the manufacturing process. The least problematic issue is the impact of ferroalloy enterprises in the water bodies. Let’s consider the situation with the impact of ferroalloy enterprises on the environment by the example of Zaporizhye Ferroalloy Works (ZFW).
In 2010 at ZFW, construction of a system of gas treatment facilities, combined with heat recovery system began. It is a dry gas cleaning system (currently, the company operates a wet gas cleaning, its efficiency is 70%, while dry gas cleaning system gives 99%). The cost of gas treatment construction building is estimated at 100 million hryvnia. The emissions must be reduced 650 times due to the installation of new sack filter instead of wet gas cleaning system, which was construed in the mid-1960s. This system mounted on the waste treatment plant should moreover give more heat to Zaporizhya homes obtained in the process of ferroalloys production .
However, the introduction of a new treatment system has faced difficulties – gas treatment facilities are being built for those of ZFW shops, which was stopped due to unprofitable production because of high electricity prices (this happened because of transfer of ZFW from the first-class of power consumption to the second one). Thus, irresponsible actions of individual public bodies (ZFW transfer to the second class of power consumption, with effect from 1 January 2011) not only lead to a drop in production at the plant, but also to the impossibility of compliance with environmental events. It should be added that the use of modern gas-cleaning equipment at ZFW would ensure compliance with the requirements of environmental and nature protection legislation of Ukraine, as well as regional programs of the getaway from ecological crisis.
Ukrainian environmental legislation is unduly harsh, including issues of time out to parameters set in it, that can be illustrated by the Nikopol Ferroalloy Plant (NFP).
The company has permission for air emissions valid till January 1, 2016. At the same time there have been problems both to obtain permits for emissions, and with the fulfillment of the conditions of this permit. The first thing to focus on is the formation of measures for the construction and modernization of the gas cleaning systems to ensure emission standards of the system, adopted by order of the Ministry of Environmental Protection № 309 of 27 June 2006. Grounding for timing of these activities is not regulated by law. As a result, the company had to make considerable efforts to ensure that, when issuing pollution permits, to prove authorities of the Ministry of National Resources, that in the conditions of current production is objectively impossible to build and commission 12 gas cleanings ($ 150 mln. each, with total capacity of 7.8 million cubic meters of treated gas per hour) for 6 years. As these figures are 1.5 times higher than that achieved for 25 years of business in this area.
Another problem for the ferroalloy producers is adopted by MNR (Order № 309) standards of maximum allowed emissions (MAE) of carbon monoxide (CO) at 250 mg / cubic meter, which has created significant problems for the company within the legislative field. The problem for NFP has never existed in principle, as maximum permissible concentrations in atmospheric air of settlements did not take place actually. With the adoption of standards for maximum allowed emissions at the national level and the issuance of emission permits under the new system (Order № 108 of the Ministry of Natural Resources, March 9, 2006), enterprise faced a problem with carbon monoxide emission limit (250 mg / cu. m) which for the ferroalloy and agglomeration productions, as well as for the steel industry as a whole, could not be achieved. This is confirmed by letter of the National Academy of Sciences of Ukraine (№ K-48-20 dated May 20, 2011).
This standard was taken into account by the State Administration of Environmental Protection in the Dnipropetrovsk region in the NFP resolution on the emission, with effect from 1 January 2011. At the same time, as for other similar enterprises of the region more sparing periods for transition to the new emission standard of CO is set. In particular, for Ordzhonikidze MPE –2012 year, Southern MPE – 2013, for steelwork “Arcelor Mittal” -2015. Metallurgical enterprises in other regions have even more time to bring carbon emissions under the established standards. There is no logical and legally valid argument that NFP is put into the most tight time frame.
The plant made significant efforts to resolve the issue (since 2008): in terms of the development of technological standards for allowable emissions as a standard which has priority over a set of 250 mg / cubic m., with the “Energostal” institution, Ministry of Industrial Policy of Ukraine, Association “Metallurgprom” Morzeev Institute, Ministry of Natural Resources of Ukraine. But, since this mechanism is not properly regulated by law, there is no procedure for its development and approval, the problem was not solved.
Current solution to this problem (by analogy, not with the help of normative documents) is in development and approval by the Ministry of Natural Resources of technological standards for permissible emissions of agglomeration (period of introduction – not earlier than 1st quarter of 2012) and ferroalloy production (the most realistic of the tight deadlines – a year 2012).
In general, today the potential risks and problems of environmental issues can occur in any enterprise in connection with the existing legislative framework. So as to air aforementioned in Order № 309 unrealistic emission standards are set, terms of achievement of which shall be established by the territorial bodies of the MNR in its sole decision, without regard to any statutory criteria. Concerning the development of technological standards of permissible emissions there is no order (or instruction) for the method of working out, necessary approvals, method of approving, the possibility of their development by individual enterprises, in case of failure of their development by entire industry. Moreover, there is no clear legally valid list of the best technologies for purification of waste gases, as well as the terms of their introduction.
It is worth mentioning the fact that the method of calculating the size of damages for violations of environmental regulations (Order № 639 of Ministry of Natural Resources t, December 10, 2008) allows to sue to any company by calculation method, regardless the actual release. The principle “polluter pays” in this case doesn’t count because the fact that there is pollution no longer required. The Law “On Air Protection” clearly establishes that the damage is calculated on the basis of the law. In our case, an order of the Ministry of Natural Resources is equal to a law.
Effective Resolution of the Verkhovna Rada of Ukraine on suspension and banning of the equipment is outdated, contains inconcrete constructions, which are absent in the laws and regulations. This allows one to use this mechanism without sufficient justification. A similar situation is observed in the sphere of monitoring the implementation of determining the effect of productive activities on the environment. Legislatively provided for execution of this work including by enterprises (Article 40 of the Law “On Environmental Protection”, Cabinet of Ministers of Ukraine decree № 391 dated March 30, 1998), however, there are no uniform requirements, organization of interaction, order of monitoring performance by the state regulatory bodies, monitoring entities, local governments, especially regarding the creation of a single automated system.
Negative social effect of infringing the interests of domestic producers of ferroalloys
As a result of rising energy costs (due to the transfer to the second class of consumption) for 8 months of 2011 ZFP had to fire 1400 employees. Because of it social tension in Zaporozhye and regions is growing. In Zaporozhye region number of people employed in mining and metallurgical complex is about 70 thousand people, and if we consider their families, then it is at least 210 thousand people, whose fate and well-being are directly dependent on the metallurgical industry. According to economists, the consequences can be very unpleasant – “Because of the forced reduction of output in ferroalloy plants and MPEs in Ukraine there is a reduction of workers. Protests are likely “says Maxim Shein, chief investment strategist at IC” BCS. “
Inadequate tariff policy, excessively stringent environmental requirements, excessive loyalty with respect to increasing imports of ferroalloy production, led to a 20% reduction in the average salary at ZFP. The total reduction in salary budget per year is 93.6 million hrn. Payments to the city budget of Zaporozhye as a tax on income of private persons reduced per year is 8.64 million hrn. Reducing contributions to the Pension Fund and other social services will be 31.2 million hrn. Increasing pressure on the employment fund will be 33.6 mln. hrn. There are disturbing trends and the NFP, which is seriously considering transfering to a four-day work week starting from November 2011.
“With the rise in price of electricity and, consequently, reducing profitability of the production of the leading enterprises of the country the shops began to be closed, work of ferroalloy furnaces is being stopped (subsequent launch of which is quite consuming process). In addition, there is a reduction of personnel, which in its turn leads to increased load on the employment center for mandatory payments to laid-off workers “- says head of corporate ratings agency” Credit Rating “Alex Chernorotov.
Summary of research
Distinctive features of Ukrainian ferrous metallurgy, predetermines its vulnerability to the crisis are the following:
1) The export orientation;
2) the high price of energy (gas and electricity) and the prospect of further improvement;
3) a significant delay modernization programs compared to advanced economies (and even compared to Russia).
All these factors need to take serious measures of state regulation and state support of industry (especially considering its contribution to filling the state budget). But in practice, we see an opposite picture.
The current situation with electricity tariffs for a number of large industrial customers (including – for the ferroalloy plants), excessive environmental demands placed upon them, the uncontrolled growth of imports of ferro-alloys, led to the fact that Ukrainian producers of the products from the domestic market displace foreign competitors. If the Ukrainian government intends to support domestic producers, then the situation – the import of ferroalloys for the forced stop domestic ferroalloy enterprises – can not hold it.
Ukrainian metallurgical enterprises are interested in the immediate vicinity of ferroalloy enterprises, which in proper time, with the required quality to fulfill the long-term contractual obligations to supply ferroalloy production. Such conditions of the steel industry can provide only domestic ferroalloy plants.
Activation of the import of ferroalloys, which occurs against the backdrop of the complicated conditions of the Ukrainian ferroalloy plants, leads to negative consequences, both for industry and for the interests of the state as a whole. The growing dependence of Ukrainian metallurgical enterprises of imported ferroalloys has led to the loss of state control over the pricing of ferroalloy products. Its price depends on the rate of return of foreign producers of ferroalloys.
In a fast changing market no confidence in the rhythm of imports. At the same time, due to the displacement of imports, domestic production of ferroalloys, Ukrainian producers are forced to cut back production. In the event of a sudden cutoff of imports to the Ukrainian ferro-alloy steel mills, domestic producers of ferroalloys objectively will not be able to saturate the market in a short period of time. The result may be a temporary suspension of work of Ukrainian metallurgical plants.
May terminate their employment and domestic processing plants, which, in turn, are already feeling the negative effects of reduced demand for its products due to displacement of Ukrainian ferroalloy imports (an essential part of production is the raw material for GOKs ferroalloy production).
Further increase in imports of ferroalloy production in the near future may lead to irreversible disastrous consequences for the domestic ferroalloy plants. Foreign competitors Ukrainian ferroalloy plants are initially advantageous position, since most of them the cost of electricity is 2-2.5 times lower than that of domestic enterprises (the production of ferroalloys objective is energy-intensive – the proportion of electricity costs on average about 45% production costs).
Because of the uncontrolled increase of imports, replacement of the domestic market of domestic ferroalloy products, Ukrainian manufacturers of ferroalloys, to avoid stopping companies are forced to sell their products for export at a price that is below cost (incurring additional losses in the form of high transportation costs). This leads to a deterioration of already difficult economic situation of the Ukrainian producers of ferroalloys. The result of conservation of the upward trend of imports of ferro-alloys will be to reduce revenues to the state and local budgets, the Pension Fund, the aggravation of the social situation in some regions (where the enterprises are ferroalloy-forming).
Connivance of growth in imports of ferroalloys results in a decrease of the industrial potential of the country, de-industrialization of the Ukrainian economy in connection with the worsening economic situation of domestic producers increased its dependence on the volatile situation and slabopredskazuemoy international commodity markets, reducing its competitiveness in the international arena.
In order to support domestic producers Cabinet advisable to hold a special investigation against imports of ferro-alloys, as stipulated by the Law of Ukraine “On the application of special measures in respect of imports into Ukraine”, based on which mode to introduce import quotas ferroalloys in Ukraine.
Resumption of routine loading of ferroalloy industry enterprises will lead to additional contributions to the state and local budgets, the pension fund. Recovery in output is in direct proportion to the reduction of tariffs for electricity for producers of ferroalloys, the establishment of sound ecological requirements for them, and restrictions on imports of ferroalloys.
The results of the expert survey conducted in preparation for the study
“Current state, problems and prospects for the ferroalloy industry of Ukraine”
The survey was participated by representatives of the following structures:
– Committee of the Verkhovna Rada of Ukraine on Energy, Nuclear Policy and Nuclear Safety
– Committee of the Verkhovna Rada Committee on Labor and Social Policy
– KPMG
– Deloitte & Touche
– Credit rating agency “KreditReyting”
– Phoenix IR Sapital
– IC “Troika-Dialog”
– IR Concorde Capital
– IC “Veles Capital”
– IR Eavex Capital
– IR “Art Capital”
– IC Kinto
– IR “Prospect Investments”
– IR BG Capital
– FG “BCS”
– International Center for Advanced Studies
The results of the survey
1. The index of investment attractiveness of Ukraine fell by 0.95 points – to the level of 2.56 on a 5-point scale. Depth of the fall of the index in just one quarter – from 3.39 in the II quarter of this year is impressive. Do you think that one of the reasons of the investment attractiveness of Ukraine index fall is the monopoly pricing of energy, including Electricity?
– No – 14%
– Probably not – 21%
– Yes – 43%
– Probably yes – 22%
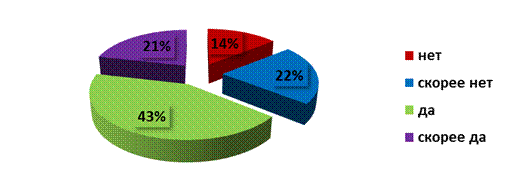
2. In the I half of 2011 the volume of imports of ferroalloys was 51.38% of the domestic market. Do you think that there are signs of importers expansion? Is this a dangerous trend for the domestic ferroalloy industry?
– Yes – 100%
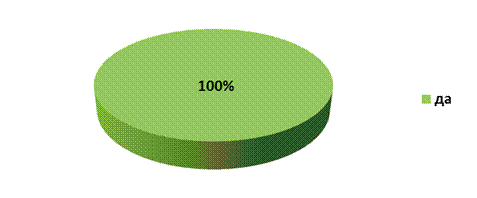
3. Due to the high electricity prices, Ukrainian ferroalloy enterprises are forced to reduce production. Because of it demand for Ukrainian MPEs production is being reduced. Do you think that may in a result cause falling of investment attractiveness of Ukrainian mining industry?
– No – 43%
– Yes – 50%
– Probably yes – 7%
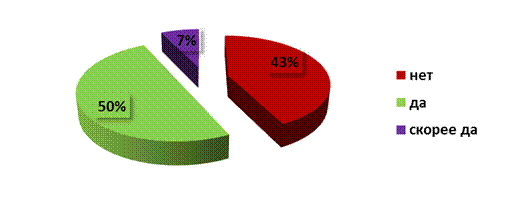
4. Because of the increase of ferroalloys imports, the demand for foreign currency rises along with payments on import contracts. Is this policy of the state, which results negative trade balance of Ukraine and creates additional devaluation pressure on hryvnia, correct?
– Yes – 14%
– No – 72%
– Probably not – 14%
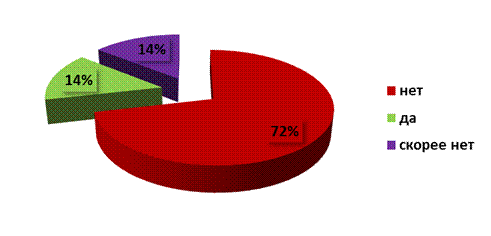
5. In Ukraine, there is an economically destructive effect as monopoly opaque pricing for electricity. Do you think it appropriate to transfer to direct contracts between producers and consumers of electricity, as prescribed by the EU Third Energy protocol?
– Yes – 100%
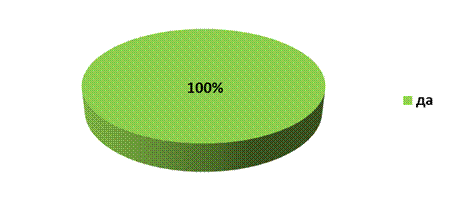
6. Due to the forced reduction of energy consumption by ferroalloy enterprises volume of production of electricity will be reduced. Can we expect some deterioration in the economic situation of producers and suppliers of electricity, reduction of their investment attractiveness (including – in the light of the scheduled for the end of the year privatization of power generating and distribution companies)?
– Yes – 29%
– Probably yes – 7%
– No – 64%
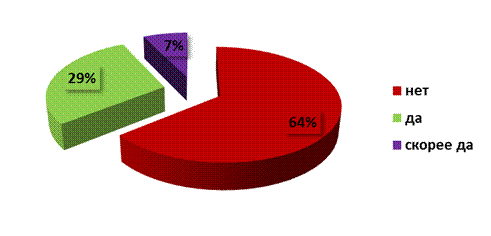
7. Getting electricity according to the second consumer class, Ukrainian ferroalloy plants now pay 0.11 dollars per 1 kW. At the same time, for example, BHPB Meyerton (South Africa) pays 0.058 dollars per 1 kW, Eramet Marietta (USA) – 0.0424 per 1 kW, Ferroatlantica (Spain) – 0.0631 USD per 1 kW, Sabayek (Saudi Arabia) – 0.032 dollars per 1 kW. Whether in such circumstances, Ukrainian ferroalloy enterprises are able ones to compete with foreign?
– Yes – 64%
– No – 36%
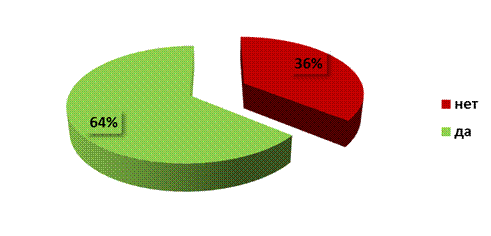
8. From the point of the interests of the Ukrainian economy is it worth introducing the practice of granting differential tariff for those industrial electricity consumers, who consume large amounts of electricity by technological necessity?
– Yes – 79%
– Probably yes – 7%
– No – 14%
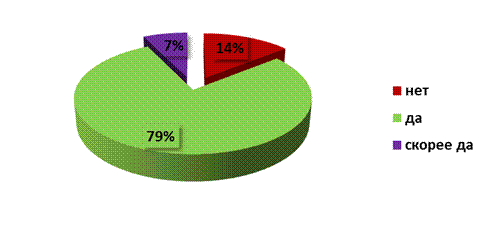
9. Through the high electricity prices, Ukrainian ferroalloy enterprises have to reduce production. Now the share of ferroalloys imports in the Ukrainian market exceeds 50%. It is projected in 2012 it could grow to 85-90%. Is the policy of the state, which creates artificial difficulties to domestic ferroalloy producers, correct?
– No – 92%
– Yes – 8%
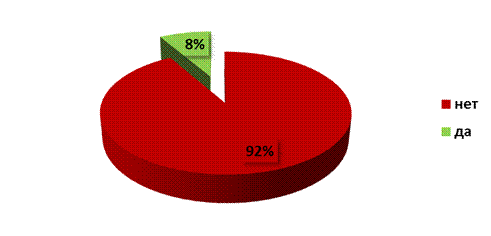
10. Because of the forced reduction of output in ferroalloy plants in Ukraine revenues to the state and local budgets are reduced, revenues from taxes on personal income are falling, the load on the employment fund increases. Is the policy of the state, resulting damage to state and local budgets, correct?
– No – 92%
– No more – 8%
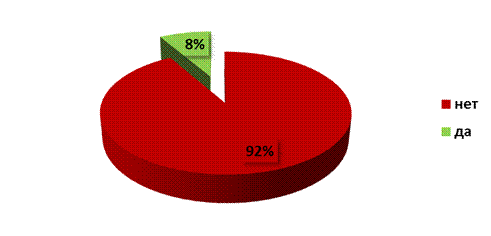
11. Because of the forced reduction of output in ferroalloy plants in Ukraine and MPEs there is a reduction of workers. Protests are likely. Is the policy of the state, resulting deteriorating social conditions in some regions of Ukraine where ferroalloy plants and MPEs are forming enterprises, correct?
– No – 84%
– No more – 8%
– Yes – 8%
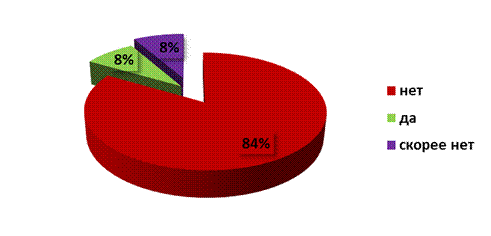
12. Because of the increase of ferroalloys imports, the demand for foreign currency rises along with payments on import contracts. Is this policy of the state, which results negative trade balance of Ukraine and creates additional devaluation pressure on hryvnia, correct?
– No – 59%
– Probably no – 8%
– No answer – 33%
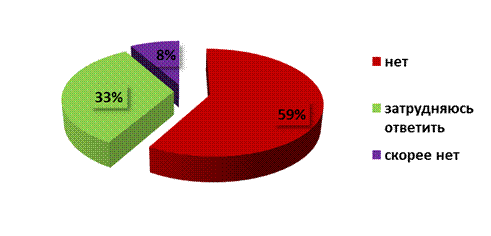
13. State support for energy-intensive industries (including ferroalloy enterprises) has been used successfully in civilized countries. Do you think it advisable to establish special low electricity tariffs for the Ukrainian ferroalloy plants?
– Yes – 66.6%
– Probably yes – 16.7%
– No – 16.7%
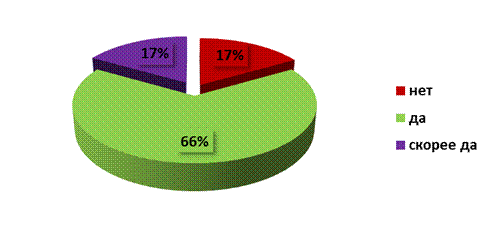
14. Through the high price of electricity domestic ferroalloy plants have reduced its consumption. At the same time, the Ukrainian electric energy is exported at a price which is 3 times lower than that domestic ferroalloy enterprises pay. Is this situation normal from an economic point of view?
– No – 58%
– Yes – 42%
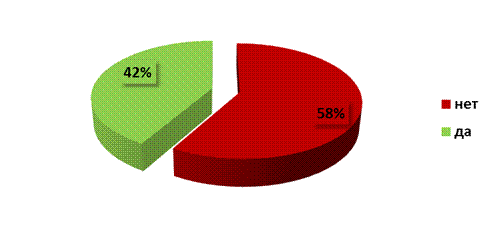
15. Do you think an adjustment policies of the state in terms of actual (not unfounded) support of domestic producers is needed?
– Yes – 92%
– Probably yes – 8%
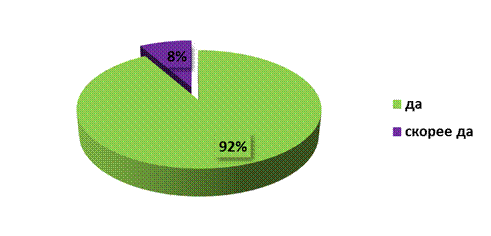